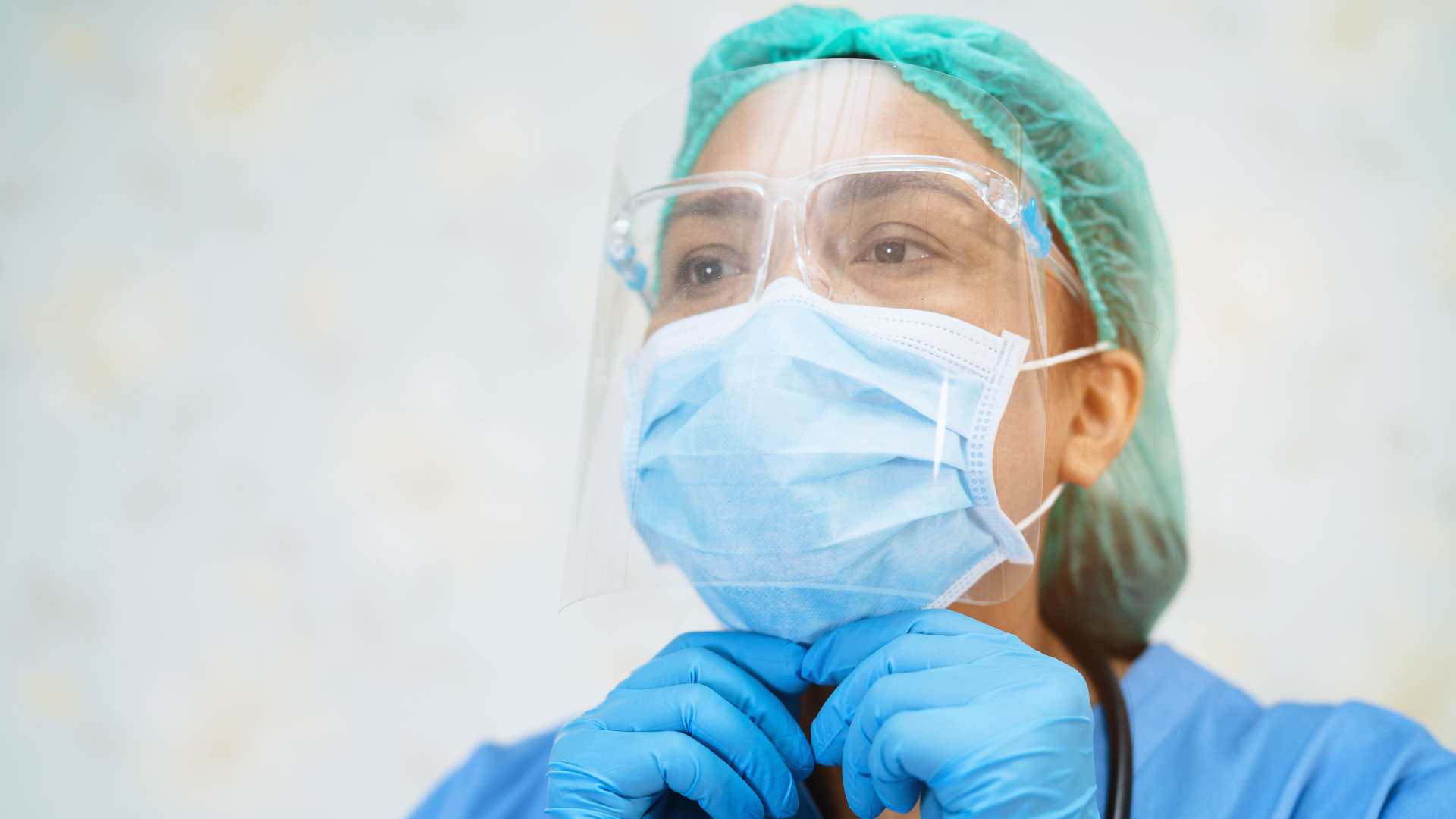
Why PPE is Essential in Any Lab Setting: Ensuring Safety and Compliance
In any laboratory setting, the use of personal protective equipment (PPE) plays a vital role in ensuring safety. Hazards in labs can range from chemical spills to biological agents, making it imperative for individuals to wear appropriate gear. PPE not only protects individuals from potential injuries and illnesses but also promotes a culture of safety within the workplace.
The importance of PPE extends beyond personal safety; it creates an environment where teamwork and productivity can flourish. When individuals feel secure in their surroundings, they can focus on their tasks without undue worry about their well-being. Furthermore, proper utilisation of PPE serves as a reminder of the potential risks associated with laboratory work.
Awareness and adherence to PPE guidelines are essential for mitigating accidents and health issues. By prioritising protective gear, laboratories can significantly reduce the likelihood of incidents, benefitting both personnel and research outcomes. Understanding the importance of PPE is the first step toward cultivating a safer, more efficient laboratory environment.
The Purpose and Importance of Personal Protective Equipment in Laboratories
Effective use of personal protective equipment (PPE) in laboratories is crucial for minimising exposure to potential hazards. By understanding its purpose and implementing it alongside risk assessments and established control hierarchies, a safer working environment can be achieved.
Understanding Personal Protective Equipment (PPE)
Personal protective equipment encompasses various items designed to safeguard laboratory personnel from potential hazards. Common types of PPE include gloves, lab coats, goggles, face shields, and respirators. Each type is tailored to protect against specific risks, such as chemicals, biological agents, or particulate matter.
Selecting appropriate PPE involves considering the specific tasks performed, environmental conditions, and the nature of potential hazards. Proper fit and comfort are also essential; if PPE is uncomfortable, individuals may be less likely to wear it consistently. Effective training on PPE usage ensures that all personnel are aware of the correct procedures for donning, doffing, and maintaining their equipment.
Risk Assessment and Hazard Identification
Effective risk assessment begins with identifying potential hazards present in the laboratory environment. This process involves evaluating chemical, biological, physical, and ergonomic risks associated with laboratory activities. Identifying hazards early allows for the development of strategies to mitigate risks.
Once hazards are identified, the degree of risk can be assessed based on exposure likelihood and potential consequences. This evaluation helps in determining the necessary PPE required to protect laboratory personnel. Regular reviews of risk assessments ensure that any changes in practices or equipment are considered and that PPE remains adequate against evolving risks.
Hierarchy of Controls and PPE as a Last Resort
The hierarchy of controls is a systematic approach for minimising workplace hazards. It prioritises strategies as follows: elimination, substitution, engineering controls, administrative controls, and finally, PPE.
Elimination involves removing the hazard entirely, while substitution entails replacing it with something less dangerous. Engineering controls include physical modifications, such as fume hoods or safety barriers. Administrative controls encompass policies, procedures, and training to reduce risk.
PPE should be regarded as a last line of defence when higher-level controls are not feasible. This underscores the importance of combining PPE with other safety measures to enhance overall laboratory safety.
Types of Personal Protective Equipment and Their Uses
Personal protective equipment (PPE) is crucial in a lab setting to ensure safety and compliance with health regulations. The following sections outline various types of PPE, detailing their specific uses and importance in protecting individuals from potential hazards.
Protective Clothing and Lab Coats
Protective clothing, including lab coats, serves as the first line of defence in laboratory environments. Typically made from materials resistant to spills and contamination, lab coats protect skin and personal clothing from harmful chemicals and biological agents.
Lab coats should fit properly, offering full coverage while allowing ease of movement. They often feature a button or snap front for easy removal.
It is essential to choose lab coats made from appropriate materials, such as cotton or polyester blends, depending on the specific hazards present. Regular cleaning and maintenance are vital to ensure continued effectiveness.
Gloves and Hand Protection
Gloves are an essential component of PPE, safeguarding hands from chemical exposure, biological agents, and sharp objects. Different types of gloves, such as latex, nitrile, and vinyl, cater to various laboratory tasks.
Nitrile gloves, for example, provide excellent chemical resistance and are preferred in many settings. They should be inspected for tears before use to ensure maximum protection.
Proper glove usage includes wearing them whenever handling hazardous materials and changing gloves frequently to avoid contamination. It is also vital to practice correct disposal methods after use to maintain laboratory safety.
Respiratory Protection and Masks
Respiratory protection is critical in labs where airborne contaminants may pose a risk. Face masks and respirators help filter harmful particles, vapours, and gases from the air.
N95 masks are commonly used when there is a potential for exposure to hazardous substances. These masks ensure a snug fit and are designed to filter out at least 95% of airborne particles.
For more hazardous environments, full respirators with interchangeable filters may be necessary. Regular training on the proper usage and maintenance of respiratory protection is essential to ensure effectiveness.
Eye Protection: Goggles and Safety Glasses
Eye protection is crucial in laboratory settings, where splashes, flying debris, or chemical reactions may occur. Protective eyewear includes safety glasses and goggles, each designed for specific applications.
Safety glasses provide basic protection but may not fully seal around the eyes. In contrast, goggles offer a tighter fit and are essential when working with volatile substances or hazardous materials.
It is essential to select eyewear that meets occupational safety standards. Regular cleaning and inspection of eye protection devices ensure they remain effective and condition-free.
Face and Head Protection: Shields and More
Face shields provide additional protection against splashes and impacts in laboratory environments. They are particularly useful when conducting experiments that involve potential explosions or vigorous chemical reactions.
Face shields are often worn in conjunction with safety goggles to provide comprehensive eye and face protection. They should be adjustable for a secure fit and made from materials that resist impact and chemical damage.
Head protection may also include caps or helmets in specific scenarios, particularly in laboratories with heavy equipment or overhead hazards.
Specialised PPE: Biosafety Cabinets and Full Body Suits
Biosafety cabinets are specialised workspaces designed to contain biological materials and protect the user from exposure. These cabinets provide a sterile environment and are essential for handling infectious agents.
Full body suits offer maximum protection in high-risk environments, such as those involving hazardous chemicals or biohazards. Made from impermeable materials, these suits ensure complete coverage of the body.
Proper training in the use and maintenance of both biosafety cabinets and full-body suits is vital to ensure safety and compliance with health regulations. Regular inspections and certifications of equipment are necessary to maintain effective safeguarding measures.
Implementation of PPE in Lab Settings: Best Practices
Implementing effective personal protective equipment (PPE) practices is crucial for maintaining safety in laboratory environments. The following best practices focus on the fit and appropriateness of PPE, training programmes, and the maintenance of equipment, ensuring compliance with safety standards.
Effectiveness of PPE: Fit and Appropriateness
The fit of PPE is essential for its effectiveness. Ill-fitting equipment can compromise safety by allowing hazardous substances to enter. Each lab should conduct a risk assessment to identify the appropriate PPE types, such as gloves, goggles, and lab coats.
- Sizing and Adjustment: PPE must be properly sized for each individual. Adjustable straps or elastic components allow for a better fit, minimising gaps.
- Material Selection: PPE materials should be appropriate for the specific hazards present. For instance, chemical-resistant gloves are necessary when handling corrosive substances.
Regular checks should be conducted to ensure PPE remains compliant with safety regulations. Employees should be educated on selecting and using the correct PPE based on their specific tasks.
Training Programs for PPE Usage
Effective training programmes are vital for promoting safe PPE usage in the laboratory. Training should encompass:
- Understanding PPE Types: Personnel need to know the differences between various PPE and the scenarios in which each should be used.
- Proper Donning and Doffing Techniques: Training must include how to properly put on and remove PPE to prevent contamination.
- Behavioural Training: Workers should be instructed on the importance of wearing PPE consistently and how to identify when it is necessary.
Regular refresher courses can reinforce knowledge and address any updates in safety protocols. Tailoring training to specific roles within the lab maximises relevance and compliance.
Maintenance, Cleanliness, and Waste Management
Proper maintenance and cleanliness of PPE are essential for durability and safety. Regular inspection schedules should be established to identify any signs of wear or damage.
- Cleaning Procedures: Lab personnel should follow guidelines for cleaning reusable PPE based on the material and contamination risk.
- Storage Protocols: PPE should be stored in designated clean areas to prevent contamination. Clearly labelled storage solutions help in maintaining organisation.
Disposal of damaged or single-use PPE must comply with waste management regulations. All personnel should be trained on proper disposal methods to ensure safety and environmental compliance. Regular audits can help maintain these best practices across the laboratory.
Role of Supervisors and Leadership in Laboratory Safety
Effective laboratory safety relies significantly on the actions and responsibilities of supervisors and leadership. They play a crucial role in ensuring compliance and facilitating education, which are vital for maintaining a safe laboratory environment.
Ensuring Compliance and Adequate Resources for PPE
Supervisors are responsible for enforcing safety regulations regarding personal protective equipment (PPE). They must ensure that all staff have access to appropriate PPE that meets relevant safety standards. This includes gloves, goggles, lab coats, and respiratory protection, depending on the hazards present.
Regular audits and inspections should be conducted to assess compliance. Supervisors must address any gaps in PPE provision and report deficiencies to upper management. This proactive approach prevents accidents and promotes a culture of safety. They should also communicate the importance of using PPE consistently during experiments.
Continuous Education and Ergonomics in Lab Safety
Training programmes are essential for reinforcing safety protocols in the laboratory. Supervisors must ensure that all personnel undergo regular training sessions covering the correct use of PPE, biosafety procedures, and emergency response plans. These educational efforts help to reduce risks associated with laboratory work.
Furthermore, ergonomics plays a key role in laboratory safety. Supervisors should assess workspaces to minimise the risk of repetitive strain injuries and ensure that equipment is accessible and safely operated. This not only protects employees’ physical health but also enhances productivity and morale in the workplace. Regular workshops and feedback sessions can further support continuous improvement in laboratory safety culture.
Comments (0)